Hope isn’t naïve optimism—the belief that some technological breakthrough will save us. It's the belief that what we do matters. That by working together, we can create a better world.
Our People, Our Impact
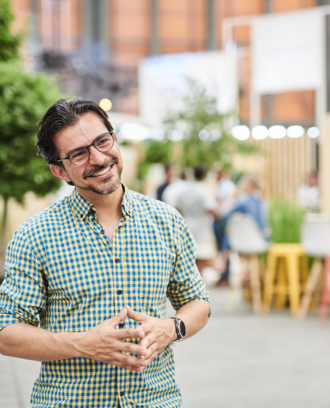


By the numbers
-
550+
# of Sustainability Certificate alumni in our community.
-
290+
Completed 'S-Lab' projects with leading companies.
-
200
# of students enrolled in our courses in 2022.
Our People, Our Impact
By the numbers
-
650+
# of MIT Sloan Executive Education sustainability alumni
-
13
Years we've offered our Sustainability Certificate at MIT.
-
600
Total attendees at the 2023 MIT Sustainability Summit.